As the construction industry enters its digital era, processes and methodologies need to be reviewed and renewed. Lean construction is nothing new, but the technology that can assist us is evolving and allowing us to benefit from easier, better, faster and cheaper delivery of our projects.
The first words that will come to mind as soon as we mention lean is “reduced waste”, and when we consider that around 57% of construction spending equates to waste and around 70% of construction projects are delivered over budget or late, it is no wonder that lean methodology is taking a more prominent stance.
What is waste? We could look at many areas:
- Poor Design
- Poor Constructability
- Poor Layout
- Excessive Staff
- Poor Procurement
- Lack of Flow of Work
- Lack of Co-ordination
- Poor Planning
- Inefficient processes
- Inefficiency in Machinery working
- Wastages of Materials
- Overrun in Time
- Overrun in Cost
- Disputes
- Arbitration
- And so on...
If we simplify this into 3 main points, time, quality and cost, we can begin to put in methods and procedures to assist in our delivery from design through construction and to effective handover. We should also consider that these three elements must be appropriately balanced because we cannot have all three at the same time. An increase in quality will result in high cost or time, a reduction in time will reduce costs but also our quality will be affected. So, a balance of these three elements, along with a defined process is where we should be starting.
The process is another interesting subject:
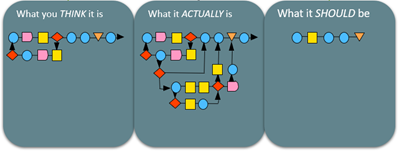
Image coutesy of Turner & Townsend
More often than not, what we usually get involved with is what is described as “what it actually is” in the diagram above, and the way we manage delivery can be reactive. Looking at the following diagram, we traditionally spend around 60% of our time firefighting problems and issues on site. Many of these issues should have been resolved during previous stages of project delivery, mainly in the design stages. In this case, we could begin to look at continuous improvement procedures and think of our future strategies going forward. But we need to get lean through the design and construction stages, allowing us the time back to change our construction delivery.
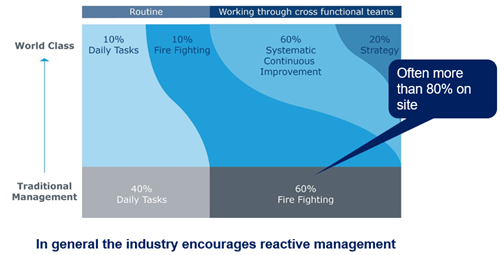
Image coutesy of Turner & Townsend
Starting with design, we need to look at how we work more collaboratively, from the initial modelling of our existing environments or buildings. This enables us to have a better and clearer understanding of what and where we are working, from point cloud surveys to laser scanning with drones, technology is making the capture of the data and translating this into valuable insight a daily norm.
We can utilise this data alongside our new virtual environments to enhance co-ordination and begin to work collaboratively in a single cloud environment. As changes occur, the whole team can become instantly aware of any potential impact on their environment or work package.
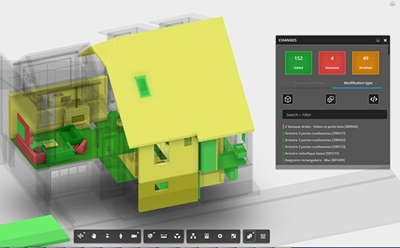
Image showing design changes in the model on BIM 360 DOC
Gone are the days where BIM co-ordinators had to setup rules and searches to group elements for clash management tests. We are now moving to automated processes to eliminate the issues presented on site where the firefighting use to take place. Automated clash detection is grouping similar clashes and presenting them in a platform that all parties have access to, allowing them to resolve the co-ordination issues in a live environment.
Autodesk’s BIM 360 platform is one of the solutions available in the market today that is changing the way we work and design our world together in a single eco-system. The platform also covers the construction sector, utilising the now co-ordinated design to enhance this data into fabrication detail and information required for manufacture and fabrication. This is what’s giving the industry the confidence to move more and more into off-site modular construction, knowing the defects have been resolved and the virtual representation of the project has been agreed before any construction takes place.
We then start to look at the individual packages of work and the components that make up that work package delivery, and why these elements should be any different to items we order online from the likes of Amazon. We should be aware when components have been manufactured, when they will be delivered to site, if they’ve been installed, and whether they’ve been signed off by the relevant party for the relevant stage of acceptance.
This is all possible in the BIM 360 platform. By using barcodes and asset tagging we can produce status reports on the components and monitor progress against the construction plan and obtain live analytics. This will result in highlighting early risk warnings for late delivery or elevating actions that need to be taken out on site.
The data captured out on the site via mobile media devices can help drive graphical information, provide live 4D models and a dashboard to monitor project performance.
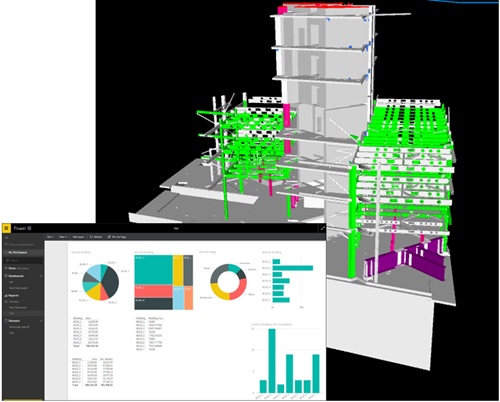
Graphics and analytics monitoring progress in delivery
By implementing technology and defining processes, we can look to eliminate waste, but there also needs to be a focus on the behaviours of our workforce. Robots were not introduced to factories overnight, we need to take small steps together through continuous improvement and leadership and embrace the changes in our industry today.
If you would like to learn more, please contact us