These solutions are now named:
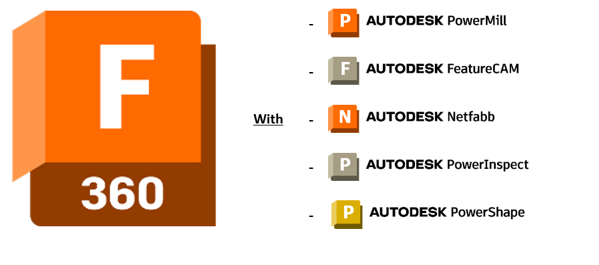
Autodesk Advanced Manufacturing Solutions Overview
The following information gives a brief overview of the solutions available in the Autodesk Advanced Manufacturing portfolio:

Fusion 360 with PowerMill is Autodesk's flagship CNC Milling solution and comes in two different versions. These are Fusion 360 with PowerMill Standard and Fusion 360 with PowerMill Ultimate.
Fusion 360 with PowerMill Standard provides CNC/CAM Programmers with comprehensive tools required for 2.5D milling, 3-axis machining, 3+2 (5-axis positional) programming and turning with excellent machine simulation and toolpath verification.
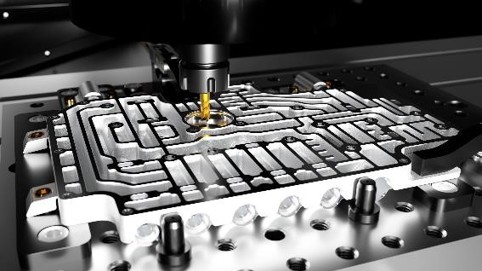
Fusion 360 with PowerMill Ultimate provides CNC/CAM Programmers with all of the functionalities found in the standard version, but it has enhanced functionality that includes but is not limited to 5-axis simultaneous programming with automatic collision avoidance, robotic programming, Electrode Manufacture (Electrical Discharge Manufacturing - EDM) Hybrid Manufacturing (DED & FFF additive processes) workflows and more.
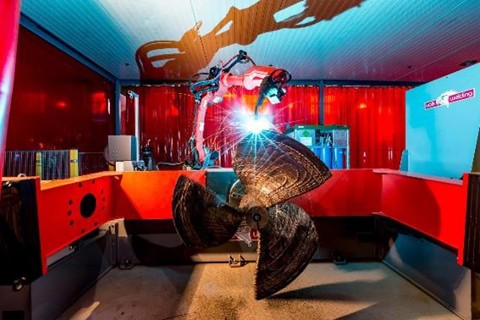

Fusion 360 with FeatureCAM helps manufacturers automate their CNC programming tasks, as it uses built-in manufacturing knowledge, accessed with intelligent decisions making, wizard-driven workflows that allow the automation of desired toolpath strategies that produce industry-leading results by eliminating repetition and minimising errors whilst helping maximise efficiency.
Fusion 360 with FeatureCAM offers toolpath strategy automation of the following types of machining:
- 3-axis to 5-axis Milling functionality.
- CNC Lathe Machining.
- CNC Turn Mill Machining.
- Swiss Lathe Machining.
- Wire EDM.
Each of the above Fusion 360 with FeatureCAM workflows are verified with the use of specialised simulation tools required to visualise programming within the machining envelope required by the manufacturer.
FeatureCAM comes with modelling tools that allow the user to generate 2D and 3D geometry needed to programme relevant CAM strategies required to machine complex components. Users can also import CAD model geometry in several file types and quickly apply toolpath strategies to machine any given component. Now under the Fusion 360 branding, CAM engineers have more tools (see Fusion 360 Modelling for Manufacture) to help with model creation and setup of complex work holding configurations.

Fusion 360 with Netfabb offers a complete toolset for designing, simulating and implementing additive manufacturing techniques (3D Printing/Rapid Prototyping). This solution comes in two different versions, Fusion 360 with Netfabb Premium and Fusion 360 with Netfabb Ultimate.
Fusion 360 with Netfabb Premium allows users to prepare models required for additive manufacturing. It hosts a wide range of tools needed for mesh repair, component orientation, support structuring, hollowing, latticing, packing and slicing and ultimately, toolpath generation required to print the model.
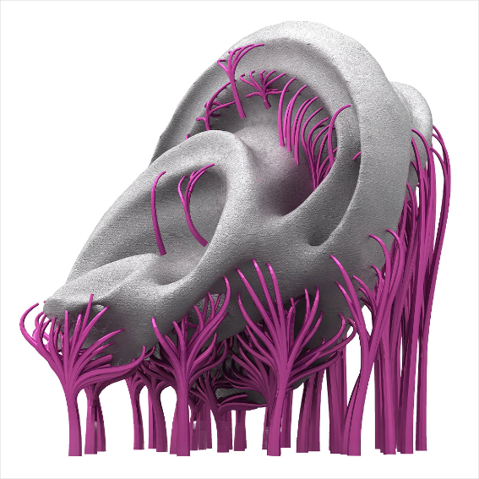
Fusion 360 with Netfabb Ultimate provides the user with all the functionalities in the premium version but has enhanced functionality that includes workflow automation, optimised lattices, limited process simulation and customised toolpath strategies.
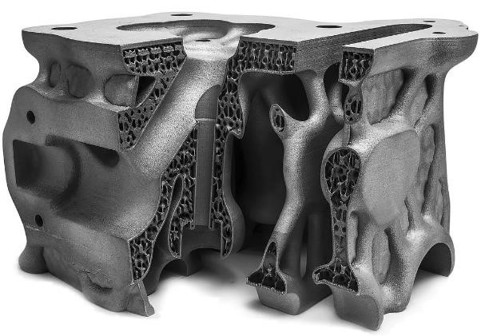
Fusion 360 with Netfabb offers various advanced additive printability solutions and boasts a growing library of 200+ integrated 3D print output formats. This allows manufacturers to streamline workflows and gain competitive advantages using automated techniques for accurate and fast results.
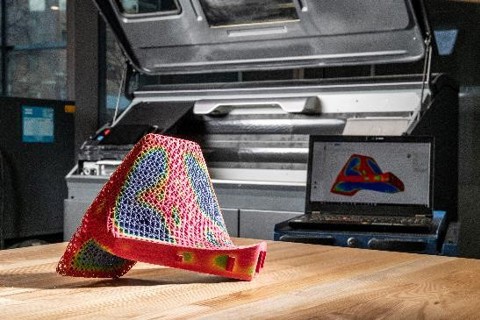
Autodesk Advanced Manufacturing Inspection Technology

Power Inspect, Autodesk’s flagship metrology data capture and analysis solution, is used when measuring complex 3D component shapes with metrology capturing hardware, aka Co-ordinate Measuring Machinery (CMM).
The solution is compatible with a wide range of CMM measurement and inspection hardware used throughout and during the inspection process, ensuring the highest manufacturing standards are achieved.
The results of this process help manufacturers speed up production times, avoid bottlenecks common to the production process and reduce scrap and rework.
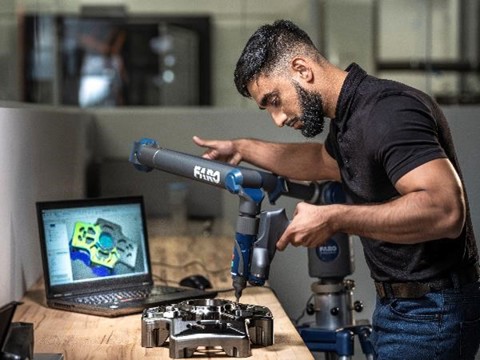
Hardware used to capture metrology related information comes in different forms and is used in different settings. These are as follows:
Contact-based CMM hardware is generally used in temperature-controlled inspection environments. This type of coordinate measuring machine (CMM) hardware comes in several different configurations, such as Bridge, Gantry, Cantilever and Horizontal Arm equipment.
Non-Contact-based metrology hardware (Optical CMM), such as Structured light 3D Scanners, capture physical geometry in the form of point-cloud data. This data is then processed and used to determine the size, variations and complex tolerance requirements of manufactured or reverse-engineered component parts.
Portable articulated arms can be set up where required and offer flexibility to the user and setting requirements. Some of these types of CMM also offer built-in non-contact-based 3D scanners making them a good hardware solution for this type of inspection process.
Machine Inspection (OMI) with spindle-mounted probes allows CNC Programmers/machinists to inspect during or at the end of machining tasks.
What is Modelling for Manufacture?
Modelling for manufacture is a critical part of the production process that could include any of the following workflows:
- Repairing Model Data
- Making the model more manufacturable
- Creating Tooling Models
- Creating accurate stock models
- Adding commonly used Fixtures and Work Holding devices and accurately locating them
- Model new features, direct model editing or deletion of unwanted features
- Representation of real-world setup in a digital environment which is crucial for accurate machine simulation
When working with Models in PowerMill or FeatureCAM the programmer may encounter circumstances where new or edited model information is required for the setup of manufacturing workflows that complement the desired toolpath strategies, collision verification techniques and simulation activities required prior to manufacturing a component.
Depending on the complexity of the desired model updates, the programmer may be required to collaborate with their customer, where the model file may have originated or perhaps even their own in-house design team. Each above option requires resources and could include a variety of engineering change processes that may result in longer design or manufacturing lead times.
What Modelling Companions are now available for use with PowerMill and FeatureCAM
- PowerMill Modelling:
PowerMill Modelling is historically the out of the box modelling companion for PowerMill Standard or Ultimate users. This modelling software gives the user a variety of surface editing tools that might be required in several modelling for manufacturing scenarios. These scenarios may include:
- Poor surface translation during the import process,
- Repairing poorly trimmed edges
- Creating capped surfaces
- Creating surface extensions for toolpath optimisation
- Surface inspection tools and techniques to ensure the surfaces being used are of a high degree of accuracy.
PowerMill Modelling is a similar, watered-down version of PowerShape. The following image shows the differences between PowerMill Modelling and PowerShape:
Products
|
PowerShape
|
PowerMill Modelling
|
Features:
|
|
|
Surface Modelling
|
Y
|
Y
|
Solid Modelling
|
Y
|
N
|
Modelling for Tool and Die
|
Y
|
N
|
Electrode Design
|
Y
|
N
|
Reverse Engineering
|
Y
|
N
|
Extract from Autodesk Knowledge Network
Fusion 360 with PowerShape is another high-end solution available from the Autodesk Advanced Manufacturing portfolio and offers advanced tools for manufacturing Tool and Die components, Electrode (EDM) Design and also extremely powerful tools required for reverse engineering activities.
PowerMill Modelling gives the user tools to perform modelling for manufacture workflows that may include:
- Creating capped surfaces
- Surface extensions
- Fixing poorly trimmed edges
- Surface inspection
Fusion 360 with PowerShape
Fusion 360 with PowerShape is the ideal enhanced modelling companion for PowerMill and FeatureCAM. PowerShape combines surface, solid and mesh modelling technology and helps engineers prepare molds, dies and a wide variety of complex parts required for production.
The high calibre modelling techniques available in PowerShape give the user robust geometry output that is required downstream for better control in CAM software, as faults found in geometry that can complicate these downstream processes can be addressed quickly and efficiently with the seamless merging of surface, solid and mesh modelling techniques.
The extensive tools and advanced workflows in PowerShape allow engineers to perform complex reverse engineering tasks such as the collection and refinement of scanned point-cloud data which is then used to easily generate and manipulate complex surface geometry in preparation for manufacture.
Now with the edition of Fusion 360 to the PowerShape subscription, users can combine all of the advanced features of PowerShape with the constantly updated, technology-enhanced, user-friendly functionality and improved performance options provided by Fusion 360.
Fusion 360 with PowerShape is now an enhanced, high-end solution available from the Autodesk Advanced Manufacturing portfolio and offers advanced tools for manufacturing Tool and Die components, Electrode (EDM) Design and is one of the best tools on the market where reverse engineering of complex components is required.
With regards to mold tools and die design and preparation, PowerShape helps automate common modelling tasks and has specialist tools required for core and cavity splitting, electrode design and manufacturing and automated Rib capping used in Electrical Discharge Machining (EDM)
Fusion 360 (with or without the Manufacturing Extension)
Fusion 360 is now available with all Advanced Manufacturing subscriptions and offers the user a cloud-based design, engineering and manufacturing platform for collaborative product development combining Industrial Design, Mechanical Engineering, Electrical PCB design and Machine Tool CAM Programming in one software solution.
PowerMill and FeatureCAM do have modelling capabilities as stated above, whether this be built-in or with the use of a modelling companion. However, now combined with Fusion 360's functionality and flexibility, these workflows and techniques are much faster and furthermore, it is simpler to use.
Fusion 360 offers solutions for the following model for manufacture scenarios:
- Poor surface translation during the import process,
- Repairing poorly trimmed edges
- Creating capped surfaces
- Creating surface extensions for toolpath optimisation
- Surface inspection tools and techniques to ensure the surfaces being used are of a high degree of accuracy.
But what else does Fusion 360 bring to the table in this field:
- AnyCAD technology (import and translation of native CAD and generic files formats)
- Mesh import and repair functionality
- Accurate Manufacturing Assemblies
- Quick creation, use and manipulation of common work-holding devices
- Minimum Radius Analysis
- Inspection Tools for Accessibility
- Version control and cloud-based storage or model data.
Take a look at Fusion 360 - What’s the Hype? | LinkedIn to see an overview of what Fusion 360 can offer a design/manufacturing team(s).
Conclusion.
So why is Fusion 360 the perfect enhancement to your Advanced Manufacturing Solution?
Fusion 360 offers manufacturers a faster, cleaner and more user-friendly approach to modelling for manufacture workflows and is an extension of their Advanced Manufacturing Solution.
With the aid of the comprehensive design tools, out-of-the-box machining functionality and advanced extensions available in each environment, Fusion 360 really does boost the manufactures potential as the solution offers some of the following directly inside the product:
- 2D, 3D and Multi-Axis Milling Strategies.
- Turning and Mill/ Turn Strategies.
- Laser Cutting Strategies.
- Additive Manufacturing Strategies.
- Inspection Technology.
- Fabrication Related Workflows including Nesting Facility.
- Access to a free Post Processor Library.
- Access to a Free Machine Simulation File Library.
- Easy to Use Machine Builder functionality for CAM-related toolpath simulation.
And more, much more!!
If you would like to discuss advanced manufacturing solutions, please get in touch and book an appointment with us by completing the form on the right,