Nastran was developed in the ’60s for NASA, with the name derived from NASA's STRUCTURAL ANALYSIS. It has been used within the industry for 40+ years and now features within the manufacturing portfolio in the Autodesk Product Design and Manufacturing Collection. The application requires a separate installation, but it is embedded within the Inventor design application under the environment tab.
Pros
- Wide variety of analysis studies including Non-linear, Fatigue, Thermal Stress and Impact
- Additional material properties included Linear, Non-linear, Fatigue and Thermal Stress
- Additional Sub-case studies for a wider array of results and load conditions
- CAD-Embedded within Inventor, with Nastran Editor also included as a standalone application
- Inspect laminar stress levels via the use of section view
Cons
- No geometry control on convergence settings
- Report Generator currently supports only Linear Static, Linear Buckling and Normal Modes Analysis types
Inventor Stress Analysis
Inventor Stress Analysis is a very useful tool to ensure that a design performs satisfactorily under expected use without breaking or deforming. There are two analysis types available; Linear Static and Modal Analysis. Stress Analysis does not require an additional installation, as it’s included within Inventor Professional under the environment tab.
Pros
- Parameter-driven optimisation included within the analysis study
- Geometry control on convergence settings.
- Simple workflow
Cons
- Limited to Linear and Modal Analysis study types
- Simple material characteristics for Linear Analysis
- Cannot inspect laminar stress levels with section view
Analysis Comparison
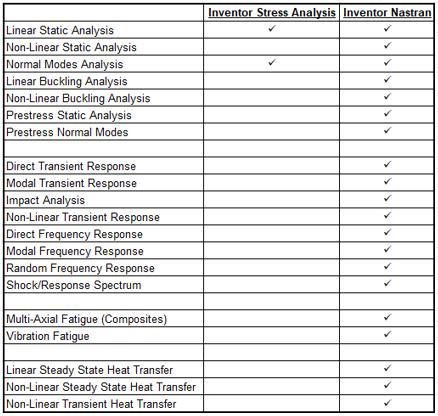
Material Comparison
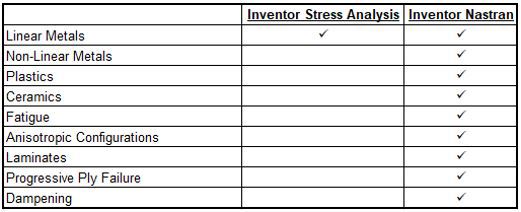
Interface Comparison

Ribbon Layout
Inventor Stress Analysis

Inventor Nastran
Browser Tree
Inventor Stress Analysis
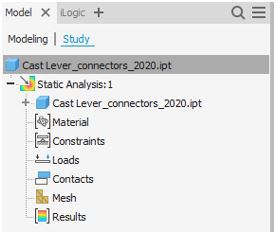
Inventor Nastran
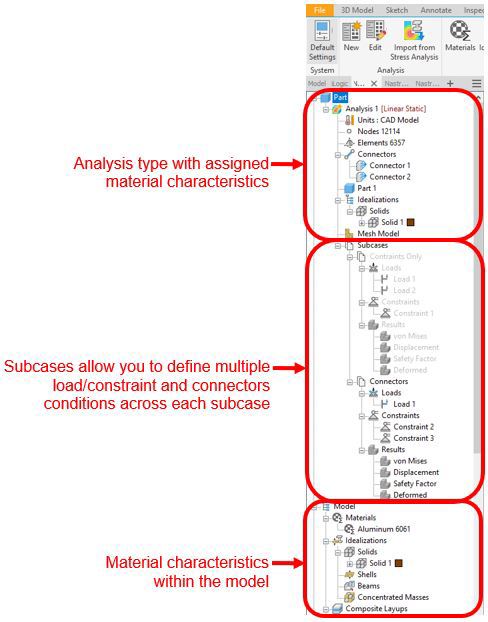
Inventor Stress Analysis
The analysis below is showing how the lever would deform under load with two-pin constraints acting as pin components, but without a specified contact, point defined along the axis.
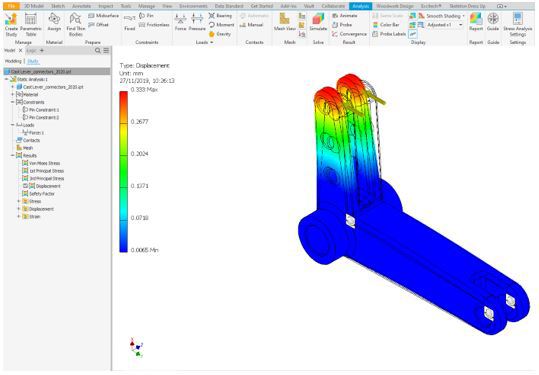
Inventor Nastran
The analysis below is showing how the lever would deform under load with two connectors acting as pin components but have been constrained centrally (Z axis) to the lever to replicate its contact point.
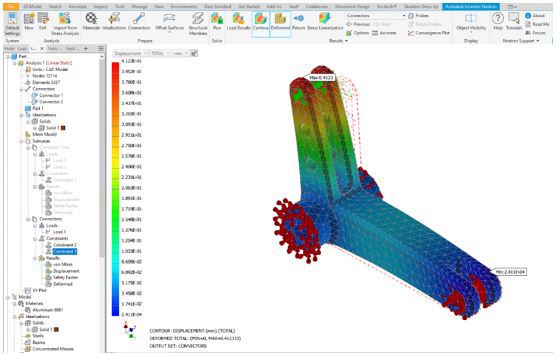
Conclusion
Nastran is included in the Product Design and Manufacturing Collection, so cost is not a factor when deciding which application is most appropriate. Using Nastran for the scenarios also available within Inventor Stress analysis will not necessarily give a superior result. However, Nastran will provide a greater range of verification tools. I could use either Inventor Simulation or Inventor Nastran for analysis to check if a component is likely to fail under a static load. The result might show no component failure, but it’s possible that buckling could have occurred before the failure point and this is where Nastran could be used to add further understanding of how our design will behave.
Nastran capabilities continue to develop within the Inventor environment. The 2020 release included Frame Analysis, Hydrostatic Load, Mesh Convergence, New Constraint Types, iLogic Support and improved Vault integration. The workflow between both applications is very similar. A positive for current users of Inventor Stress Analysis when needing to use Nastran for additional analysis types.
Autodesk users needing to understand and prove the viability of their design have access to two great desktop tools within the Design Collection. That capability is supplemented by Fusion 360 with access to cloud-based simulation, giving access to the almost infinite processing power to offload the burden from the desktop.
Regardless of the scenario, the tools available at the design stage within the Product Design and Manufacturing collection, empower engineers to make early informed choices reducing downstream costs and improving efficiency.
At Symetri, we offer a full range of services to complement these tools and enable you to take full benefit of the possibilities that are available.
In addition to product training, our experts can partner with you to help you apply those skills to your specific scenario, helping you to design the best product for manufacture, environment and cost, as well as form and function, regardless of application.
Take a look at our simulation training courses available to you.
To discuss how Symetri can help you achieve your design objectives, fill in the form, and we will contact you.