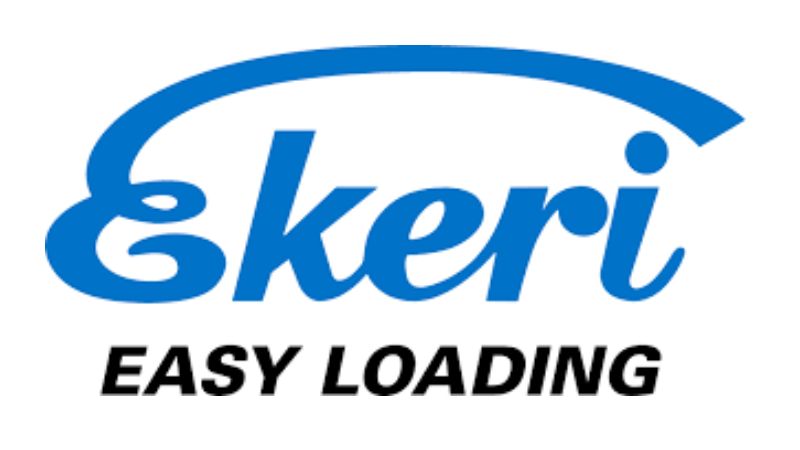
Learn how Advanced Oncotherapy is using PLM to achieve and sustain ISO compliance and FDA validation
Challenges
- Cost: they were developing many of our business processes from scratch.
- Wanted a platform to enable them to control the business without mounds of paperwork
- Their goal was to expand beyond the traditional PLM functionality of managing the product and include other areas such as quality and non-conformity.
- Initially looked at expanding the use of their previous PLM system as it contained some of the functionality required, but it came at an extra cost.
Solutions
- Fusion Manage was the best solution, as you can access all its capabilities for a single license fee
- Advanced Oncotherapy commenced its implementation in late Spring with the assistance of D2M3, a consulting firm and Autodesk partner. Within 3 months, they had transferred all of the data and went live with the basic components.
- D2M3 provided the training and support and helped to improve their understanding of Fusion Manage and ultimately refine their processes. D2M3’s commitment to the project was excellent
- Previously, Advanced Oncotherapy only had six users on its legacy PLM system. By taking advantage of the additional capabilities available in Fusion Manage, the company expects that everyone in the organisation will eventually have access to the system.
Benefits
- One-stop shop for evidence of business processes and reporting
- Currently using Fusion Manage for Audit Management, Goods Receiving, Customer Complaints, Change Control, Intellectual Property Management
- Working towards complete integration of PDM, PLM, and ERP activities to minimise administrative work and reduce risk of errors
- Long-term objective: All master data and ‘objects’ in one place for ease of audit