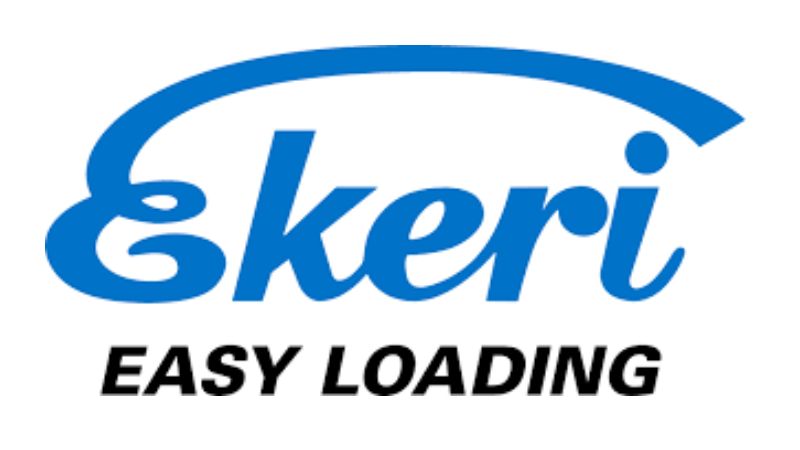
Delivering confidence and quality faster: Sotech’s adoption of Altair® SimSolid® aligns product output with client expectations closer than ever before
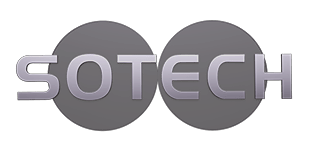
Meet Sotech
Established in 1982, Sotech is a leading designer and manufacturer of engineered metal rainscreen cladding and architectural fabrications, marketed as the Optima range.
Sotech’s team works closely with architects, installers and contractors to specify rainscreen cladding solutions appropriate for each individual project. Sotech provides expert advice on the system, materials and finishes, fire safety, sustainability, design and production.
Form, fit, and function
Rainscreen cladding protects a building’s backing wall from the elements—such as rainwater and condensation—it improves thermal performance and enhances a building’s appearance.
In addition to its critical functionality, the cladding is also the ‘face’ of the building—what people see in terms of the aesthetics of the building, how it complements and enhances the built environment around it or, if required, recedes into and merges with its surroundings.
While architects always seek these qualities in an exterior surface, they also look for performance and longevity; assurances of safety and protection for the building. From the functionality perspective, a cladding layer prevents significant amounts of water penetration into the wall construction, prevents air permeability, and provides enhanced thermal performance.
Safety has always been Sotech’s primary concern, and there has been a dramatic focus on the importance of large-scale fire testing in recent years.
Sotech Optima FC+, TFC+ and Edge Rainscreen system has been tested to BS8414-2 and classified to BR135. BS8414 fire test refers to the fire performance of external cladding systems.
The fire tests evaluate whether a cladding system subject to fire breaking out of an opening (such as a window) in an external wall, will result in excessive fire spreading up the exterior of the building and the potential for fire to re-enter at a higher level.
Sotech’s Optima suite of rainscreen façade systems has been successfully tested to CWCT standards. These standards cover air permeability, water penetration, wind resistance (Serviceability & Safety) and soft and hard body impact testing.
Sotech is also accredited to ISO9001:2015, ISO14001:2015, and ISO45001.
The challenge: Reduce the complexity of ensuring accuracy
Reassurance, confidence, and trust
In his role as Sotech’s Principal Technical Engineer, Mo Jenaban spends much of his time interacting with architects to make sure that the design parameters are met in line with the architect’s vision and contractor’s design intent—from the moment it has been considered, through to the delivery on site.
“We have a great reputation in the construction sector for the quality and safety of our products”, says Mo. “A key part of my job is to consolidate and grow that reputation. Exterior cladding for buildings has been much in the news in recent years, raising the safety stakes for many suppliers. But from Sotech’s point of view, we have always been obsessed with safety, and particularly fire safety.
Providing this sort of reassurance to customers is essential in gaining and keeping their trust. So, anything that reinforces our ability to do this, merits serious consideration at Sotech”.
Physical testing cost vs value
Prior to Mo joining Sotech, the company had undertaken all its product testing physically. This had involved specialist third-party testing companies and hiring rigs for the tests. The tests were also limited in scope, being able to cope only with standard panels within certain sizes.
Mo chose to adopt Finite Element Analysis (FEA) to avoid the costs and the limitations while adding process value at the testing stage. Sotech was one of the first manufacturers in its industry to do so. Complications remained though, as FEA still requires meshing to ensure an accurate representation of a panel’s geometry.
The company commenced its search for a better solution; something to take these complications out of the structural analysis equation and speed things up. “FEA involved long lead times”, says Mo.
“While that’s going on, our client is under pressure to progress with the project. When a project is underway, it’s in everybody’s interest to keep the momentum going. Simply by working through the process of structural analysis—that we had to undertake—we had no choice but to keep people waiting. I knew there had to be a way of solving this issue”.
The Solution: Altair SimSolid | Core and central to product quality and client trust
No more geometry prep | No more meshing | No more waiting
Mo was at a RICS presentation when he met some of the team from Symetri. “I spoke with a few Symetri people and my first impression was that they understood the construction sector inside-out. They were involved with pretty much every specialist role in the AEC sector. It was an informal chat, but it made me think they could be just the partner Sotech needed to help us align our products and our design processes ever closer to the way our customers worked”.
Mo had seen some videos of SimSolid in action and was impressed by the tighter accuracy that its simulation functionality offered. “The Altair team gave us some demos and I saw the advantage right away; no more need for manual geometry preparation and meshing—exactly where all the time was being consumed.
Symetri confirmed this was the way for us to go, and have been invaluable in guiding us through the initial adoption phases to get us up and running in the shortest time possible”.
Enhancing BIM alignment
With its AEC focus, Sotech is progressively BIM-aligned, with many of its solutions readily available as BIM objects through the company’s own BIM page and NBS library. SimSolid has been a catalyst in Sotech’s ability to make its objects more intelligent.
“Using SimSolid, we developed our own stiffener matrix”, says Mo. “This takes in project-specific wind load and recommends the number of stiffeners to be used to reduce deflection. We also use SimSolid to determine stress concentration zones on panels to avoid excessive stress on the panel where deemed necessary by either looking at material thickness or enhancing fixing locations and distances. This is something we used to have to do with FEA”.
The outcome: Structural analysis is now 50% faster by
“We continue to save time with SimSolid. The time saved varies by the complexity of the projects. On average, across all projects, we’re approximately 50 per cent faster.
Time is not the only factor that has been reduced—costs are lower and site pressure has been eliminated. So, SimSolid doesn’t just provide a better structural analysis process, it enables us to deliver a better client experience. We’re closer to our customers and smarter in meeting their needs.
Whenever we’ve needed advice and guidance on SimSolid, Symetri has been there for us and we’ve also availed ourselves of their training services on numerous occasions. We know our business, but Symetri knows the software that helps drive it”.
Find out more about SimSolid structural analysis for rapid design interactions.
Challenges
- Making sure the design outcome is in line with all parties' ideas involved, such as the architect and contractor.
- Continue to uphold Sotech’s creditable reputation, especially with safety precautions and make their company further known in the industry.
- Develop testing to further avoid costs and limitations.
- Lessen lead times.
Solutions
- Using SimSolid to create the shortest lead times possible.
- Making products more BIM aligned using SimSolid.
- Finding alternatives to FEA and exploring different software solutions.
Benefits
- Overall structural analysis has become 50% faster.
- Site pressure being eliminated.
- Costs being lowered overall.
- Support from Symetri throughout when using SimSolid and needing guidance.
Related Cases
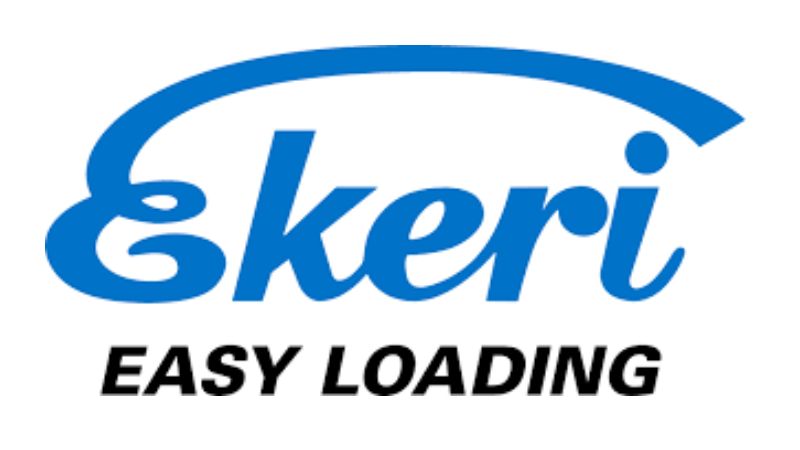
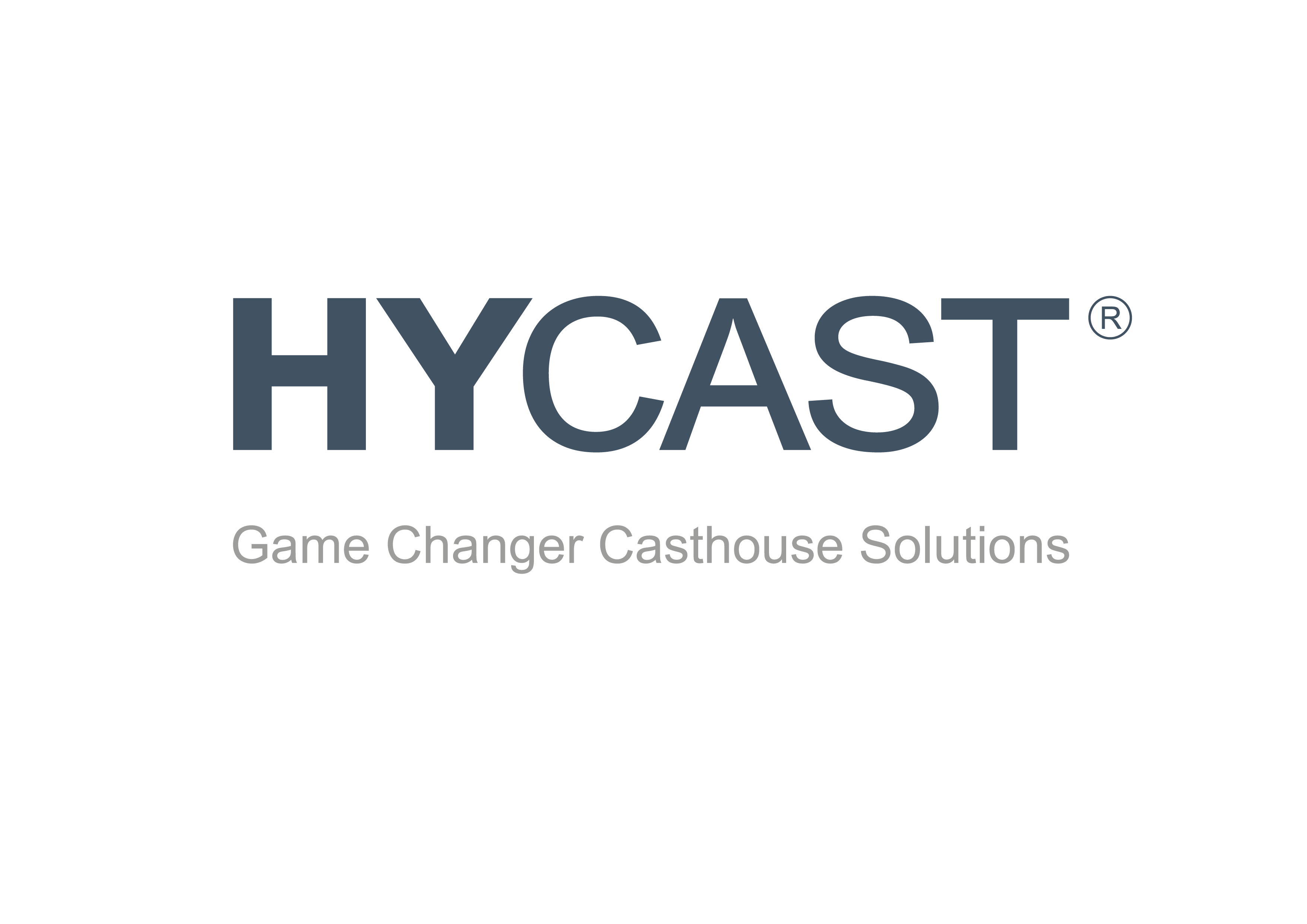
Hycast Enhances Efficiency and Collaboration with Sovelia Core
Meet Hycast Hycast provides next-generation casting technology and delivers state-of-the-art fully automated casting lines. For more than 30 years Hycast has been a leading and world-class provider of aluminium casthouse technology. Hycast is a sp... Learn more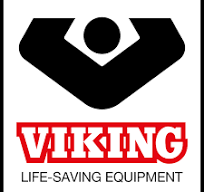