Taking the next step in innovation: Symetri Fusion 360 training for HiiROC, leaders in Thermal Plasma Electrolysis
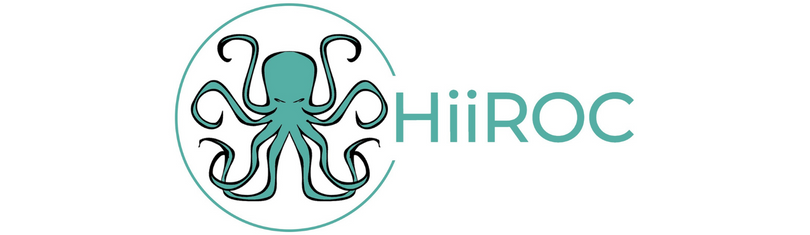
Meet HiiROC, they develop transformational technology for low-cost, zero-emission hydrogen generation. The company has developed and patented a new process for creating hydrogen, known as Thermal Plasma Electrolysis (TPE). TPE is an electrically driven-process that uses a plasma torch to decarbonise hydrocarbons, releasing the valuable, high energy density hydrogen and solid carbon black.
HiiROC was founded in 2019 in the UK, to commercialise its technology, with development and assembly facilities based in Hull, where there is ready access to engineering expertise. HiiROC’s technologies are set to make a significant impact on current climate issues.
HiiROC was named winner of the KPMG Private Enterprise Global Tech Innovator award, overcoming competition from over 1,100 applicants from 22 countries.
The Challenge: Improve and accelerate production
For machined components within the company’s plasma torches, HiiROC had traditionally sourced externally. This approach seemed logical, given the requirement for high-precision machine capabilities, however, it led to production delays since third-party suppliers could not always meet the demands of HiiROC’s fast-paced Research & Development requirements. Incorrectly machined tolerances also occasionally appeared. ‘Time-to-test’ was therefore impacted by both re-work required and lead times.
In light of these considerations—together with HiiROC’s requirement to drive down the cost per part, while maintaining the highest quality—HiiROC decided to bring all parts manufacturing in-house.
In line with this programme of continuous improvement in manufacturing processes, HiiROC invested in a HAAS UMC-750 5-axis Machining Centre, to ensure finite accuracy in the manufacture of the multi-sided and complex parts involved in the plasma torch.
Adam Lester, Inventor and Vault Engineer at HiiROC, wanted to make sure he and his team could optimise efficiencies when it came to creating multi-axis machine paths for making their own parts.
Adam had been investigating Autodesk Fusion 360, to help fulfil this requirement but wanted both reassurance that this was the right way to go and guidance in familiarisation with and then advanced capabilities in using the software.
He asked Symetri’s Advanced Manufacturing Team how to move forward.
The solution: Bespoke training in Fusion 360 to streamline the design-to-manufacture workflow
HiiROC already used Autodesk Inventor for Computer-Aided Design (CAD) modelling, with Autodesk Vault for Product Data Management (PDM) to track design changes and manage CAD data. The design team knew Autodesk products, but those on the production frontline needed to be brought up to speed on the CAD side of the requirements for CAM programming. The goal was to ensure seamless workflows, from concept to finished items.
The objective driving Symetri’s assistance for HiiROC was to ensure team knowledge and ability in the use of Autodesk Fusion 360’s manufacturing environment, helping the team to set the path for efficient manufacturing model setups, use the software to the fullest of its capabilities and deploy their machining experience further into a more automated way of machining.
Given that HiiROC had already invested in the HAAS UMC-750 5-axis Machining Centre, they approached Symetri for training in Fusion 360 and for reassurance on using this software compared to others for their machine. Symetri’s Advanced Manufacturing team advised HiiROC that there was a post-processor readily available online at the Autodesk HSM Post Library and that Fusion 360 would be the perfect CAM solution for HiiROC to achieve their goals. The only hurdle to overcome was to ensure that HiiROC’s manufacturing team became confident users of CAM Technology in the form of Fusion 360.
Symetri’s proposed training package for HiiROC covered Essentials training, 3-axis Milling and then Multi-Axis Milling in the forms of 3+2 (5-axis Positional Machining), 4-Axis Rotary Machining and 5-Axis Simultaneous Machining techniques found inside Autodesk Fusion 360 manufacturing workspace and advanced machining extension. The training was bespoke and built around HiiROC’s specific use cases. It was also built around HiiROC’s appetite for innovation and its future expectations of new machining requirements.
The training was undertaken by Symetri’s Advanced Manufacturing team, who showed HiiROC how to set up their machine inside Fusion 360 to gain five key benefits:
- The ability to generate a digital twin of their physical setup
- Applying toolpath strategies to HiiROC’s models
- Template creation for speeding up future production of CAM Models
- Toolpath simulation strategies for machining components and performing collision detection and toolpath optimisation tasks
- Exporting the machining strategies using HiiROC’s post processor to generate the NC code required to programme the HAAS UMC-750 5-axis Machining Centre.
Outcomes: Innovating faster
After the training, HiiROC reported significant improvements in manufacturing turnaround times and quality. The company subsequently purchased a HAAS DS-30Y CNC Lathe with Y-Axis Milling functionality and is looking to use Fusion 360 as the CAM software for this machine. HiiROC will be attending further Fusion 360 CAM training focused on Turning and Mill/Turn activities, allowing them to automate the programming of their new CNC lathe.
Fusion 360 is continuously updated with new and improved technology features and workflows. It will allow their new CNC Centre Lathe with Y-Axis Mill capabilities to be programmed after performing toolpath simulation, which is required for collision detection and toolpath optimisation workflows.
Related Cases
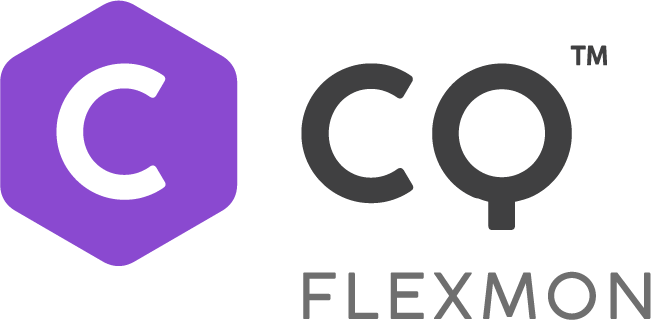
NO MORE SPIRALLING SOFTWARE COSTS - JUST DATA-DRIVEN PRECISION WITH CQFLEXMON
MEET "THE" ARCHITECTS This acclaimed design practice is known for delivering high-quality work across architecture, master planning, and interior design. With particular strengths in the workplace, lifestyle and leisure, and residential sectors, t... Learn more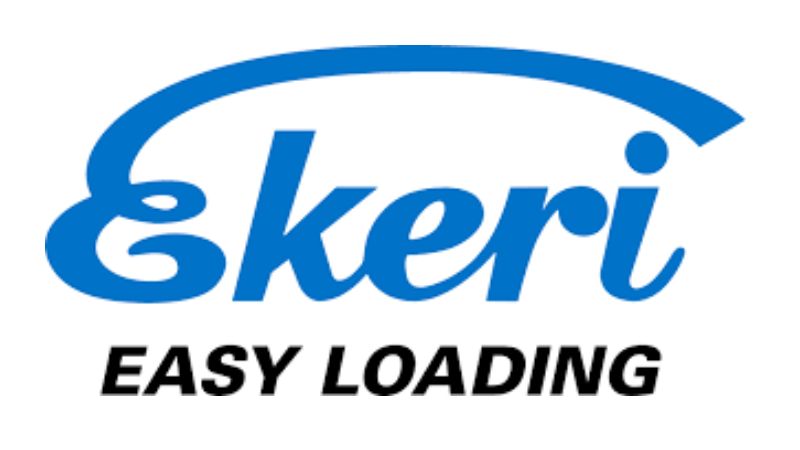