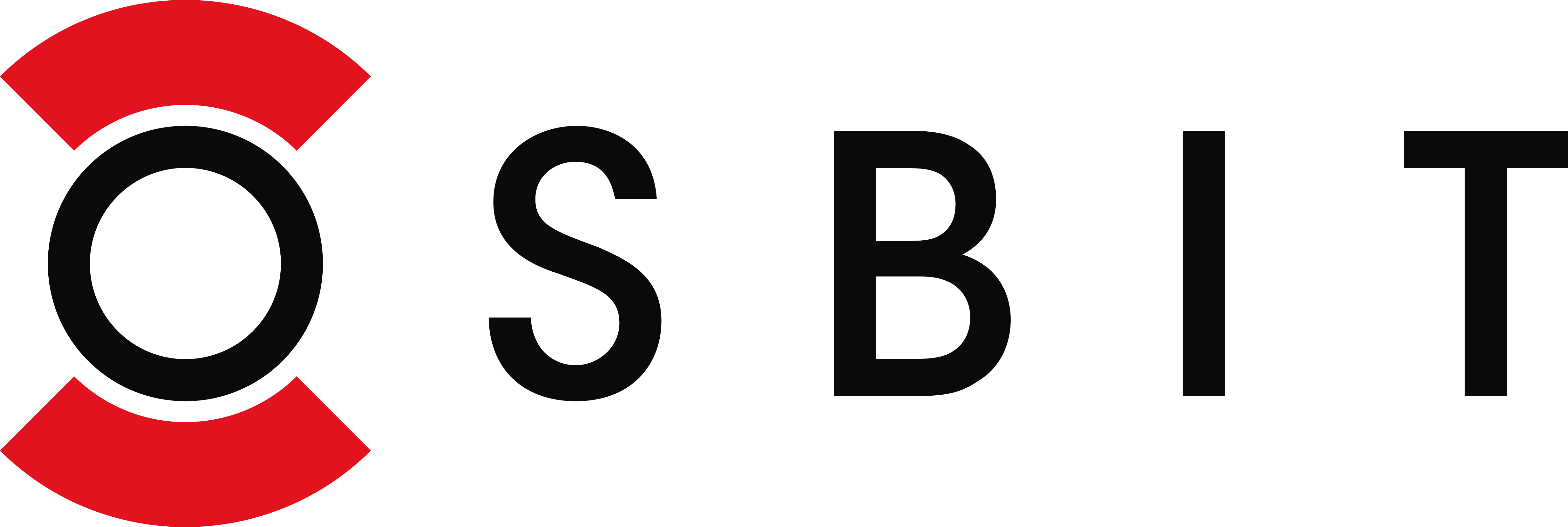
Product development time slashed by almost 70% using Altair® SimSolid®: Modulift’s design time drops from 600 to 200 hours
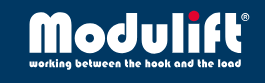
The Modulift engineering and design team are no strangers to projects with high-level QA requirements and a highly specialised focus on creating a bespoke solution. It has often been the case that the equipment they design and manufacture solves problems not usually encountered in lifting projects.
Modulift, founded in 2002, is renowned globally for manufacturing modular spreader beams, lifting beams and spreader frames.
Typical scenarios that Modulift finds itself frequently addressing include the lifting of wind turbine blades, monopiles, Oil & gas platforms, housing modules, etc. Among the company’s landmark projects were custom lifting frames for the High Speed 2 (HS2) project, a custom-made 50 WLL (Working Load Limit) lifting frame for a 20-metre long, 38-tonne wave machine, and a giant lifting rig for the lifting and assembly of 5MW wind turbines destined for the Irish Sea. Modulift also supplies equipment for Subsea Lifting and recently successfully delivered a Subsea Lifting Beam to the Baleine Project for a TBM recovery from the sea bed.
The company’s customer base ranges across construction, breakbulk and ports, shipping and maritime, offshore industries (oil, gas, and wind) and cargo, transport and logistics.
Challenge: Switching software used for a critical process, knowing that you will gain the improvements you anticipate
The pain of manual analysis and geometry preparation
Finite Element Analysis (FEA) is integral to the design process of all Modulift’s products. It is an extremely detailed analysis process. When deployed, the products are subject to bearing enormous weights – a Modulift spreader beam, for example, has capacity from 2t to 3000t – and forces brought to bear across the structure; compressive forces in the beam, tensile forces in the slings, and enormous stress on the bolted sections and links.
Historically, the Modulift team undertook all analysis of these multiple stress points manually, simply relying on AutoCAD as its principal design software. Eventually, Modulift migrated to 3-D analysis and design platforms by the implementation of Software packages such as Solidworks & STAAD Pro.
The long search for excellence
Such was the way of things when Harshal Kulkarni joined the company in 2019 in the role of Engineering Manager. Harshal’s experience was in the field of structural and mechanical design in the oil and gas and petrochemical industries.
Change is often evolutionary, however, as Harshal and the six-person engineering and design team at Modulift (seven, including Harshal) were about to discover. “The consensus among the team was that we could achieve accurate FEA results faster than was possible through a manual approach if we took on a software that was designed for the purpose”, says Harshal. “We opted for a highly reputed simulation solution together with a solution for structural analysis. They were both cutting-edge. They were both worthy of their reputation. But a problem that we hadn’t foreseen came to light”.
Harshal explains that the simulation software Modulift had chosen turned out to be highly technical. It required considerable technical skill to work with the software. Core engineering and 3D design skills were not enough, and, as a result, training new users was an intense process.
The elimination of risk
Modulift’s products and services are always in very high demand. The company fulfils a very specific requirement in heavy or complex lifting projects, many of which fall into the category of infrastructure projects. Given that many are also bespoke, a large amount of time is taken up by liaising between clients’ engineering teams and the Modulift team. Time is of a premium, and very little of it can be set aside for user training on complex software.
“After working with these solutions for some time, it was clear that the FEA workload was all channelled through one or two engineers, our experts in using the software,” says Harshal. “In 2021, these engineers left the company, so I took on the role of FEA. More specifically, I experienced first-hand the complexities of using the software. Too much risk was involved in having one competent user among a team of seven. We needed a far more accessible solution. We also needed some expert help in identifying it”.
Solution: Turn it on and use it – the simplicity of SimSolid
Geometry simplification simplified
Harshal spoke with three potential providers of three different solutions to Modulift’s problem: de-risking the FEA process and making it faster at the same time by having software that anyone on the team could use.
“I included Symetri in our enquiries since the company had been a supplier of Modulift since 2012 and, corporately, we understood the wide experience they could bring to solving problems within manufacturing”, says Harshal.
Symetri recommended Altair SimSolid as the optimum solution and one that came with the endorsement of manufacturers all over the world in manufacturing specialisations which mirrored Modulift’s. The software removes the need for the manual process of geometry simplification and produces results in ‘seconds to minutes’ as the Modulift team was about to discover.
Outcomes: Productivity has gone through the roof
Minimal training, maximum accuracy, optimum reliability
“We are at an early stage of our adoption of SimSolid, but have seen a very large change in a very short space of time with SimSolid”, says Harshal.
Freedom from Meshing Process
Simsolid does not use the Meshing Process for Finite element analysis, which significantly reduces the modelling time for analysis and avoids complex features and commands, unlike the other similar FEA programs.
The above feature makes Simsolid extremely user-friendly, time-efficient and easy to learn and gain expertise.
“We have seen design time drop from 600 hours to 200 hours on a product development project.
As we extrapolate that metric into the future, you can imagine the total impact it will have on productivity as well as enhanced ability to take on more projects”.
A fully upskilled team
“The Symetri team has made a significant difference to our design and product development processes”, says Harshal. “They won us over to SimSolid with their very first demo of the software, and there were smiles from the whole Modulift team as Symetri’s consultants took us step-by-step through the ease of use of the software.
A huge sense of relief settled on the team. We had found a solution that would relieve the stress and strain from an intense process, let alone analyse the stress and strain aspects of the products we design. It was very obvious, very quickly, that any of us could use it. At a stroke, we have expanded a previous two-man skill into a critical design skill we now all have, just by opening SimSolid whenever we need to”.
Challenges
- The pain of manual analysis and geometry preparation
- Overcome the manual analysis process
- Finding new design software to match current needs
- Setting aside lengthy training time for complex software
Solutions
- Adoption of Altair SimSolid
- Removal of the need for the manual process of geometry simplification
Benefits
- Design time dropped from 600 hours to 200 hours on a product development project
- Relieved the team of stress and strain from previous intense processes
- Design skill capabilities are now expanded across the team due to the user-friendly nature of SimSolid
Related Cases
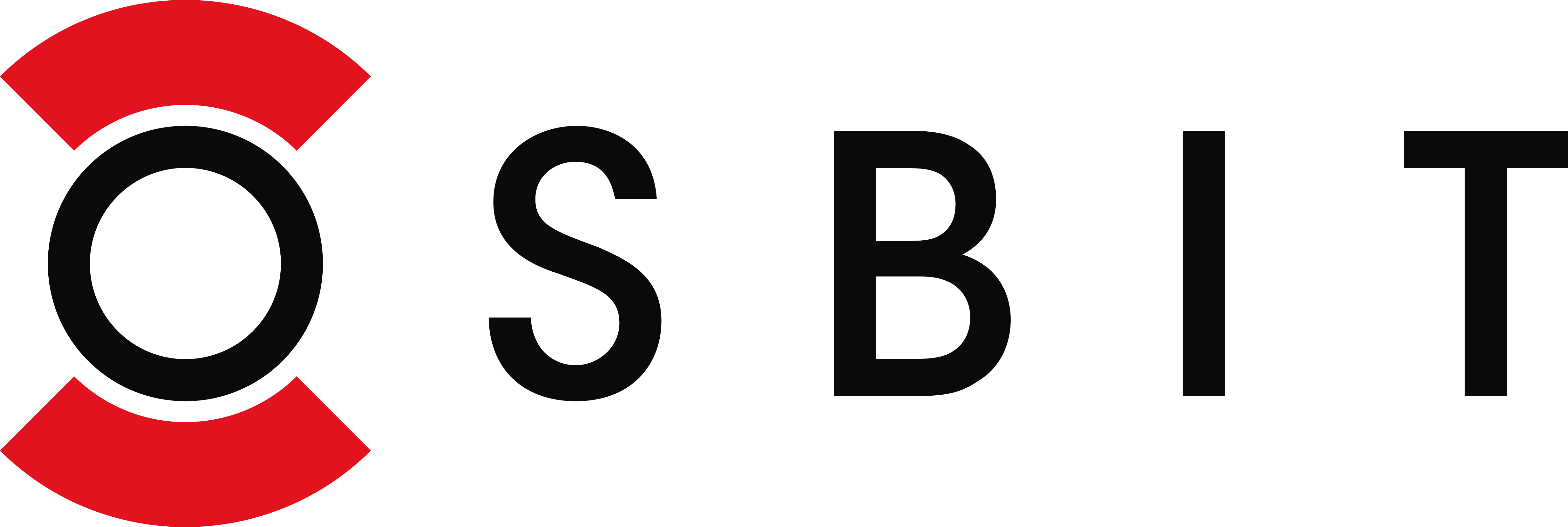
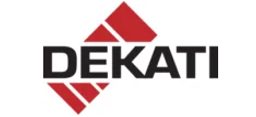
Dekati Relies on Sovelia PLM for a Seamless and Smoother Flow of Information from Design to Production
Meet Dekati Ltd They have been a world leader in designing and manufacturing innovative fine particle measurement solutions for 30 years. They provide measurement instruments and complete measurement solutions to various environments and sample co... Learn more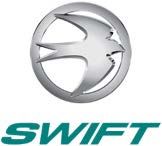