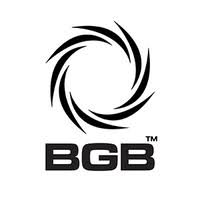
Symetri introduces Pentre Offshore Engineering to Altair SimSolid; achieving super-fast structural analysis in design
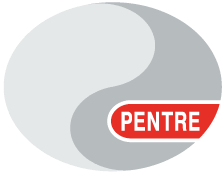
Pentre Offshore Engineering is part of the Pentre Group, formed in 1988 and now regarded as the leading manufacturer in Europe for reels, drums, spools, and ancillaries to the global wire and cable industry; any organisation involved in linear-wound products.
Headquartered in Leigh, Lancashire, Pentre Group also has manufacturing facilities in the Czech Republic and Spain. Pentre Offshore Engineering’s main focus is on the oil and petrochemical offshore environment; specifically, the design and manufacture of drums for transportation and installation, of wire ropes and umbilical cables (multi-function cables or hoses for use underwater).
The company places a heavy emphasis on in-house manufacture to provide bespoke solutions in compliance with offshore standards.
Challenge: Improving engineering design productivity
One step forward, one step back
Teddy Crockwell is Pentre Offshore Engineering’s Technical Manager, charged with making sure that the company’s design process continuously evolves to harness the benefits of new technologies. He spends much of his time with the company’s heavy industry customers; exploring their requirements in detail as part of the bespoke service proposition for which Pentre is so well known.
With regards to the specialised nature of Pentre’s products and the design processes involved in meeting the requirements of harsh usage environments, Teddy says that the company had traditionally made calculations on model geometries manually. When this approach was superseded by the practice of finite element analysis (FEA), the resultant digital efficiencies made it easier to achieve accuracy faster.
To go a step further, Pentre started to use Inventor Nastran to gain the advantage of advanced and accurate simulation. Teddy felt that the FEA process remained a challenge in itself, not in terms of its efficacy, but in terms of the time it took up with each new product or product modification.
“Our products are typically large and complex —and this requires remodelling after the inaugural design version to load the model into Nastran. In overall terms, Nastran was doing the job we needed it do in addressing the FEA process, but for our purposes, and given our project throughput, it wasn’t doing it fast enough.
No strangers to tailor-making solutions ourselves, we asked Symetri if there was anything they could do in this regard to reduce the time burden of this remodelling process”, says Teddy.
It was typically taking three to four days to re-create an ‘analysis-friendly’ version of the model for Nastran after it had originally been created in Inventor. The workload faced by Teddy and the other engineers at Pentre Offshore Engineering can run to 20 concurrent projects.
Even on the lower estimate of 3 days for model re-creation, that means that the equivalent of a rolling two months was being consumed by re-working. Pentre had accommodated the time burden because there was no choice. This made it no less frustrating for the engineers, and equally so for the welders and fabricators in the factory. It also meant that extra time was being spent on a design that was taking engineers away from new projects: “It was a case of taking one step back every time the team took a step forward,” observes Teddy. He asked Symetri to resolve the issue.
Solution: Reduced analysis times, with Altair SimSolid
Faster design iterations
Pentre Offshore Engineering had been working with Symetri since 2014—five years before Teddy joined the company—in areas both of Pentre’s CAD products (identifying appropriate solutions, software sourcing, installation and licensing) and ongoing support via the Symetri support team for all of their design and simulation products.
“Symetri was highly regarded by our whole team”, says Teddy. “I was particularly interested to hear how our team had been helped out on numerous occasions by Symetri’s technical support team, who really understand the world of manufacturing. They had wide experience of the engineer/production line interface, and the ever-increasing adoption of digitisation at each stage in making seemingly simple, yet structurally complex, products”
To address Pentre’s remodelling conundrum, Symetri introduced Teddy and the Pentre engineering team to Altair SimSolid, a structural analysis tool for use during the design phase. SimSolid analyses the inherent geometry of a model, eliminating the need for model reworking/geometry simplification. It can be used either as a standalone tool or in conjunction with Nastran.
Simulation simplified
SimSolid works directly on CAD geometry without the need for simplification and meshing. “The simplification that SimSolid brings to the design phase is what really drew us to it since our structures are thin-walled; traditionally requiring multiple element types, the source of the necessity to re-work models,” says Teddy.
“This complexity, as far as the manufacture of drums and reels is concerned, is mostly down to the thin-walled nature of our structures. SimSolid accommodates such design nuances and achieves simplification by comparing the direct geometry (Inventor files or other CAD formats) to the boundary conditions that the designer sets—in terms of constraints or loads—and then calculates local and global errors relative to these conditions via AI and algorithms.
To make sure that this new approach would provide the simplicity it promised and liberate designers and engineers from the shackles of the rework process, Symetri recommend a six-month pilot. The workflow transformation for Pentre Offshore Engineering became apparent far sooner than that.
Outcomes: 4-day process shrinks to half a day
Expanding opportunities: more customers satisfied, more of the time
Within a month of embarking on the trial period, Teddy stated that the team reported that they were impressed with the new process:
“Symetri showed us how to make the impossible possible” “Engineers now have a reliable analysis of their designs’ performance quickly; same-day—not after three to four days’ extra effort”.
SimSolid does not use an FEA method but rather a meshless method to calculate stresses and deflections. “We’re seeing other benefits from SimSolid in addition to the time saved”, says Teddy. “By gaining greater insight into design performance earlier on in its development we are able to make adjustments such as removing weight from the structure. Put simply, we can now take the already high quality of our products to a higher level, and this is a real plus in terms of our competitive advantage.
Symetri approached this project with a vengeance. They took great care in making sure that we were confident in our adoption of SimSolid. They are firm believers in knowledge transfer, and we’ve benefitted hugely from their insights, as well as the determination they showed through the trial period to leave us with a fully developed new skill across the team.
The impact on our output has been a culture change, and the benefit for our customers has done great things for our reputation in the industry”.
Challenges
- Excessive time taken to re-work models for structural analysis
- Accommodate timely design modifications for tailor-made projects
- Manual intervention for meshing issues
Solutions
- Altair SimSolid requires no mesh and geometry simplification
- Flexibility of being able to work in conjunction with Nastrans, or standalone
Benefits
- 3-4 days’ effort reduced to a matter of hours
- Cost savings resulting from fewer person-hours
- Significantly improved engineering and manufacturing productivity
- More satisfied customers, more of the time
Related Cases
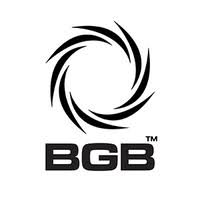